Post Updated 9/4/2024
The difference between FluidForming and hydroforming can be summarized in a single word: precision.
FluidForming hydroforming is the first significant advancement in metal forming since sheet metal hydroforming was introduced in the 1950s. Since then, manufacturers have designed products around the limitations of existing metal forming technologies. Essentially, they’ve been designing for the future with a technology that dates back to the start of the Cold War.
Times have changed. So should your hydroforming metal forming and manufacturing technologies.
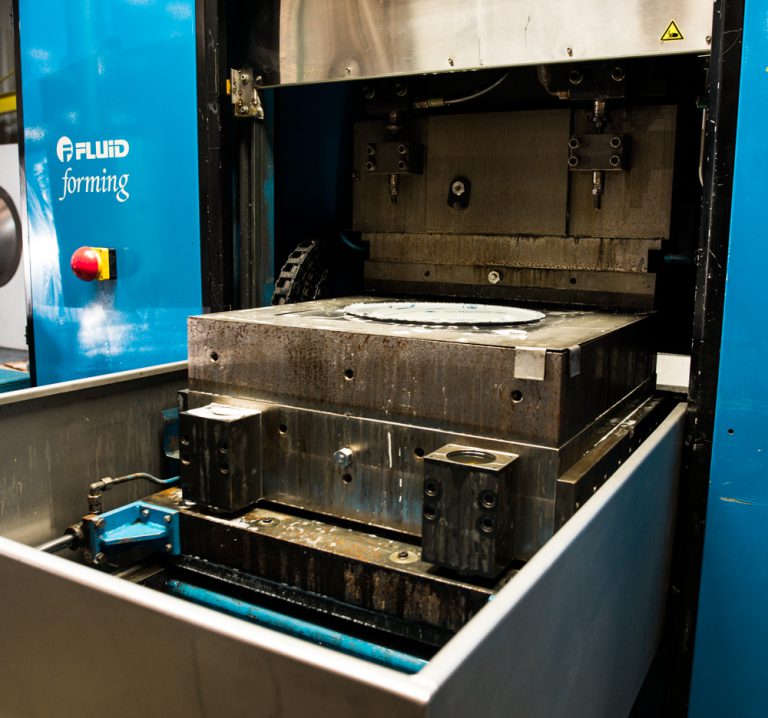
FluidForming is a precision metal forming technology that offers product development specialists, advanced manufacturing visionaries, and product designers an exciting alternative to legacy metal stamping and bladder-based hydroforming.
FluidForming -- and FluidForming Americas -- makes what was once impossible, possible.
From rapid prototyping to the production of highly-detailed premium components, the compact and self-contained FormBalancer — FluidForming Americas’ universal three-in-one metal forming machine — offers manufacturers unprecedented flexibility.
FluidForming Americas (FFA) is streamlining production and lowering costs across many different industries.
A detailed look at the difference between FluidForming and hydroforming
Better Physics
Unlike traditional bladder-based hydroforming, which uses costly and environmentally harmful hydraulic fluid to fill a rubber bladder, FluidForming’s bladder-free technology uses water as the forming force.
With forming pressures up to 4,000 bar / 60,000 psi, FluidForming is the most accurate and highly repeatable metal forming and tube forming process available to manufacturers today.
Better Surface Quality
Because of FluidForming’s extraordinarily high forming pressures (up to 4x higher than legacy hydroforming) and bladder-free technology, surface quality is not compromised by the tool or bladder surfaces that are typically used in legacy forming systems.
Since the forming fluid — pressurized recycled tap water — comes in direct contact with just one side of the sheet metal surface, there are no tooling marks. FluidForming is perfect for pre-finished materials, which improves both aesthetics and consumer appeal. Trademarks, brands, and logos can all be easily incorporated into the design of each part. Post-production finishing work is minimized with FluidForming technology.
Unsurpassed Quality, Accuracy, and Structural Integrity
With a 99.996% first-pass yield success rate, FluidForming is the only Six Sigma metal forming process available to manufacturers. FluidForming offers the quality, accuracy, and repeatability that manufacturers and product developers can rely on.
Post-production costs are minimized, part fit-up is accurate and can often be completed without the use of fixtures and jigs to hold parts in place. FluidForming’s higher forming pressures also ensure greater structural integrity. The resulting accuracy also minimizes “fit-up” issues, reduces costs to assemble the finished project, and is laser-weld ready.
Lower Costs
Thanks to dramatically reduced tooling costs, the elimination of sheet metal fixturing, and minimal tooling and equipment wear, production costs for most components are significantly lower. Because the FormBalancer is a bladder-free, closed hydraulic system that uses recycled water instead of costly hydraulic oil, maintenance costs are also much lower than traditional hydroforming or die stamping.
Our customers benefit from low ownership and production costs, thanks to dramatically reduced tooling costs, the elimination of sheet metal fixturing, and minimal tooling and equipment wear. Because the FormBalancer is a bladder-free, closed hydraulic system that uses recycled tap water instead of costly hydraulic oil, maintenance costs are much lower than traditional hydroforming or die stamping presses.
It’s worth noting that in some instances, the development of new processes or new and improved products may qualify for research and development tax credits.
The difference between FluidForming and hydroforming is clear. To learn more about this enabling technology or to see if FluidForming is right for your next production run, contact FluidForming Americas today at (800) 497-3545 or email us at info@ffamericas.com.