And what's the connection between lean and sustainable manufacturing?
Lean manufacturing (also referred to as lean production) is a business model and collection of tactical methods that emphasize eliminating waste and inefficiency while delivering high-quality products on time. The EPA notes that “in the U.S., lean implementation is rapidly expanding throughout diverse manufacturing and service sectors such as aerospace, automotive, electronics, furniture production, and health care as a core business strategy to create a competitive advantage.”
Simply put, the main idea of Lean manufacturing is to maximize value while minimizing waste. Lean means creating more value for customers with fewer resources — which lines up pretty organically with sustainable manufacturing.
What are the five principles of lean?
The goal of Lean manufacturing is to drive rapid, continual improvement in cost, quality, service, and delivery. As an added benefit, however, significant environmental benefits often occur as a result of these production-focused efforts. Lean production techniques create a culture of continuous improvement, employee empowerment, and waste minimization (EPA).
The five principles of Lean manufacturing can improve efficiency and minimize waste.
- Define value: What does the customer want, how do they want it, and how much are they willing to pay for it?
- Map value stream: Using the customer value as a reference point, map out the activities that provide value and those that don’t add value.
- Create a flow: After removing waste, ensure the remaining steps run smoothly.
- Establish pull: Inventory is considered one of the biggest wastes in any production system. The goal of a pull-based system is to limit inventory and work in process (WIP) and apply just in time (JIT) to sync with demand.
- Perfection: Continue to fine-tune and perfect processes. Continuous process improvement is a part of Lean culture.
SOURCE: Chartered Institute of Procurement and Supply (CIPS)
How can FluidForming support lean and sustainable manufacturing
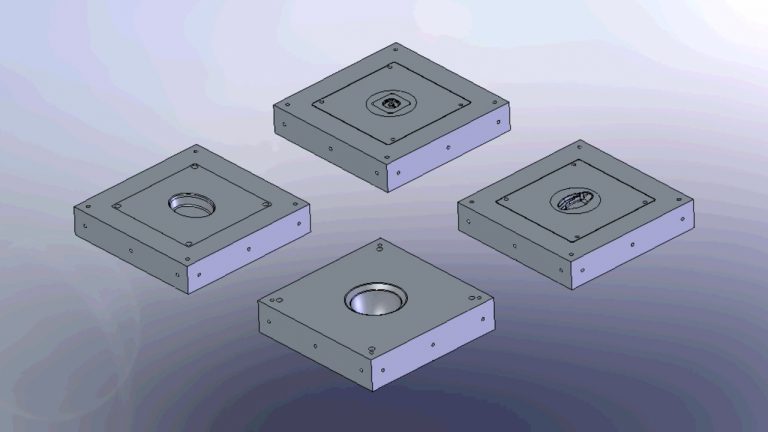
- Culture of continual improvement.
- Focus on eliminating waste.
- Offers low total cost of FormBalancer (FluidForming metal forming machine) ownership.
- Eliminate consumables like hydroforming bladders, oils, and hydraulic fluid.
- Eliminate the potential for environmentally harmful spills and leaks.
- Maximize production floor space.
- Eliminate overproduction.
- Nested tooling capabilities
- Reduce raw material waste.
- Six Sigma (99.996%) first-pass yield rate.
- Fewer defects mean less waste.
- Improve product durability and reliability.
- Increase product lifespan (reduces environmental impact while meeting consumer needs).
- Easily accommodate iteration and process improvements.
- Easy-to-maintain/low maintenance equipment.
- Increases equipment longevity and decreases the need for replacement.
- Less solid and hazardous waste.
- Reduce carbon emissions.
- Recycled tap water is the forming force.
- Right-size equipment options.
- Reduces the complexity of the production process.
Support your Lean manufacturing processes with FluidForming Americas. FluidForming is a sustainable manufacturing process that enables innovation. Contact us at 800-497-3545 or email us at info@ffamericas.com.
FluidForming Americas, Inc. is a member of the Precision Metal Forming Association and is AS9100 Rev D, ISO 9001:2015 certified.