FluidForming Americas and Advanced Manufacturing are a match made in metal forming heaven. We're living in an incredibly exciting time for manufacturing, advanced product development, advanced engineering, and precision metal forming. As the first major advancement in metal forming since the 1930s, FluidForming Americas is ready to tackle tomorrow's great ideas today.
“Let's go invent tomorrow instead of worrying about what happened yesterday.”– Steve Jobs
Manufacturing drives global growth and innovation
In both developing and advanced economies, manufacturing continues to play a critical role. In the United States, the manufacturing sector accounts for a whopping 11% of the country’s output. The sector employs over 11 million workers.
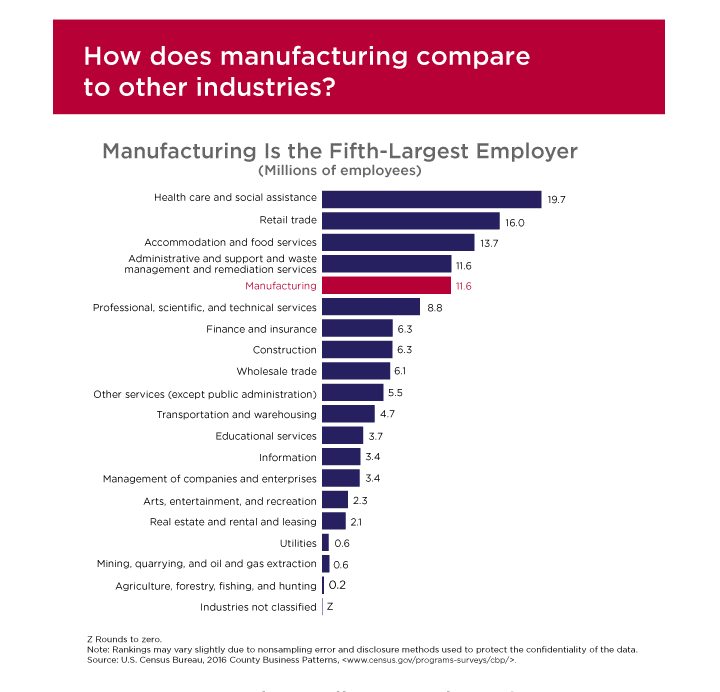
However, the global manufacturing sector has changed tremendously since the 20th century. So tighten your seatbelts, because the third decade of the 21st century is shaping up to be a tumultuous one.
Developing nations are suddenly leaders in manufacturing, recessions have damaged demand, and then booming economies have restored demand. In some places, at least. Trade wars threaten the global markets while new advancements soothe them.
That’s a bumpy ride.
The manufacturing sector has changed. Business leaders and procurement teams can’t rely on old technologies and dated methodologies in today’s rapidly evolving manufacturing space.
In advanced nations like the U.S., new technologies — like FluidForming — are paving the way for innovation, productivity growth, and new trade opportunities.
Technologies like FluidForming support innovation and advanced manufacturing
“Technology does support and drive innovation. Technological advancements can allow manufacturers to create higher quality goods faster than before, with less expense and help them realize more efficient operations to become more competitive” (National Institute of Standards and Technology).
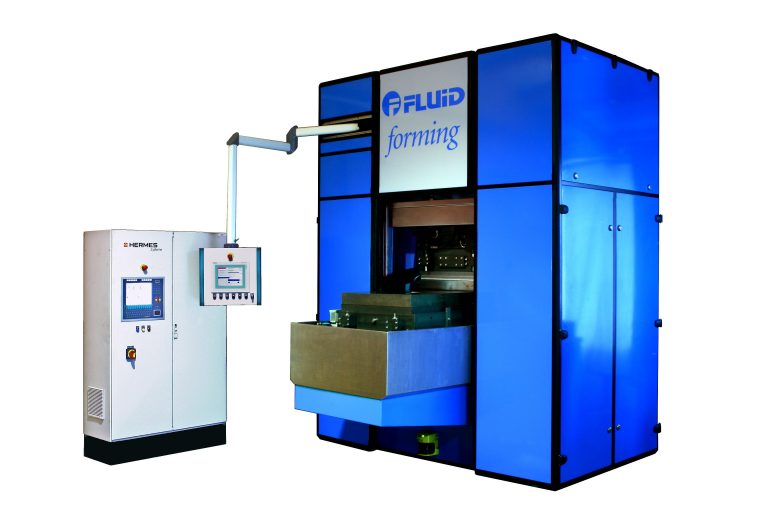
FluidForming’s family of metal forming machines — FormBalancers — seamlessly integrates several new technologies. These cutting-edge technologies are revolutionizing manufacturing innovation and disrupting the world of advanced manufacturing.
Additive Manufacturing and 3D Printing
FluidForming Americas’ 4-in-1 metal forming machines work flawlessly with 3D printed tooling; saving companies hundreds of thousands of dollars in tooling costs per part and dramatically reducing a product’s time-to-market.
With forming pressures 4,000 bar/60,000 psi, FluidForming offers unparalleled manufacturing flexibility, accuracy, and repeatability. Not only does the FluidForming technology marry additive manufacturing with metal forming, but FluidForming is also the only company to offer an unprecedented combination of technologies incorporated into a single machine. Perfect for the world of advanced manufacturing.
FormBalancers have the following metal forming capabilities and can be integrated with 3D printed tooling:
- Sheet metal forming
- Tube forming
- Bladder-based hydroforming
- Hydraulic hydroforming
“Complexity is free with 3D printing. Not so with injection molding, machining, casting, and other traditional manufacturing processes, where complex part designs make production costs skyrocket.”
— President and CEO of FluidForming Americas, Paul Benny.
Advanced Alloys
FluidForming is highly compatible with a variety of metals, alloys, and superalloys. Even aluminum alloys, which are notoriously prone to wrinkling and fracturing under stress, perform well with the FluidForming technology and process.
Finite Element Analysis
FluidForming’s finite element analysis (FEA) software accurately predicts how a product will react to real-world forces, mechanical stress, work hardening, material thinning and more.
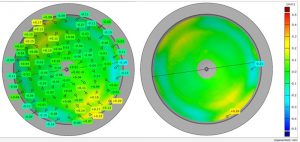
This analysis uses mathematical equations to predict — with a very high degree of accuracy — how well a component will form and function work in reality.
Data sets are easy to export and advanced manufacturing product engineers can perform in house analysis and dynamic testing of the designed part. By catching problems earlier, we’re optimizing part function and design while eliminating countless hours of lost time and the cost of failed prototypes.
So what, exactly, does FEA mean for our clients? It means that with our part simulation and modeling capabilities, we can form complex parts from metal perfectly the first time and every time after that.
FluidForming Americas is a member of the Precision Metal Forming Association and is AS9100 Rev C, ISO 9001:2015 certified.
Visit us at FabTech 2019
You'll find us in Booth D46352 at FABTECH 2019. We'll be there, in Chicago, November 11-14, showing off our Six Sigma satellite dish, microchannel heat exchanger, and so much more.
Learn more about our precision metal forming and find out if FluidForming technology is right for your next project. Contact FluidForming Americas today at (800) 497-3545 or email us at info@ffamericas.com.