Sheet Metal Forming
Six Sigma precision metal forming process for rapid prototyping & medium-volume production.
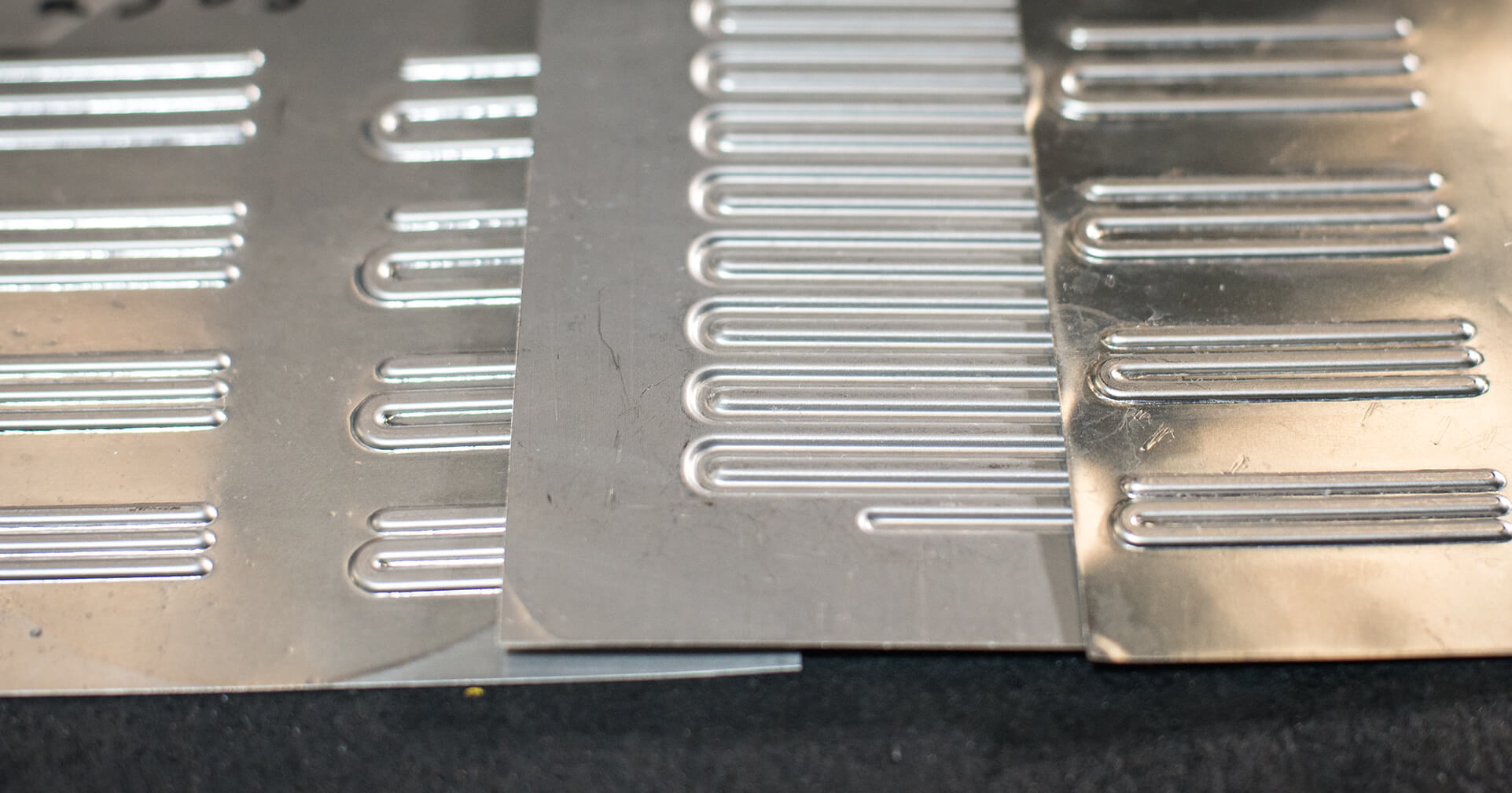
FluidForming Americas is a quality-driven sheet metal forming company that offers manufacturers a cost-effective way to quickly — and with unbeatable levels of accuracy and repeatability — produce complex shapes. We’re committed to working closely with our customers at every stage of a project’s life cycle.
If you’ve been searching for a sheet metal forming company that cares about your product and your reputation in the industry — and a metal forming process capable of helping you achieve new levels of quality and durability — then your search is finally over. We’ll make sure your project stays on schedule and on budget.
The FluidForming sheet metal forming process accommodates integrated logos, undercuts, organic forms, deep drawn parts, and even components with curves that would be likely to wrinkle or tear with traditional metal forming methods.
FluidForming sheet metal forming is designed for low- to medium-volume parts production. It’s also the trusted rapid prototyping process for product designers and product developers.
Not only can FluidForming produce parts previously considered impossible to hydroform, but it’s the only sheet metal forming process that’s compatible with prefinished, polished, patterned, and etched materials.
FluidForming is better than stamped sheet metal.
Like die stamping, or “pressing,” FluidForming hydroforming is a cold forming process. That’s where the similarities end. Stamped sheet metal is one of the oldest methods for metal forming. FluidForming is the newest.
During the metal stamping process, a sheet of metal is placed into a press where a two-part tool and die then force the metal into a desired shape.
Often, the metal must go through several progressive stampings, each using unique tooling. The process is not only time consuming and costly, but it also damages the surface of the material and weakens the sheet metal. Operating expenses, equipment maintenance, tooling and die, and post production fixturing costs are all high.
FluidForming is better. A single die is used from prototyping through finished product. And, because water is the force to form, tooling marks are nonexistent. High forming pressures ensure unbeatable accuracy and repeatability.
High-pressure sheet metal forming.
Forming and clamping pressures are independently variable throughout the entire process. As a result, the FluidForming process enables single die deep drawing. Because one cavity can be used for multiple forming stages, progressive dies are unnecessary. Which improves accuracy while also dramatically lowering tooling costs.
Once clamping pressure has been established, water is introduced into the FormBalancer (our precision sheet metal forming machine) with pressures of up to 4,000 bar (60,000 psi) — that’s more than 4x the maximum pressures typically used in legacy hydroforming!
Depending on the geometry of the component, the sheet metal can be locked in place or allowed to flow freely into the die cavity. The metal is then stretched evenly — and virtually without friction — into the cavity.
Because there are no cumbersome bladders used to contain forming forces, FluidForming’s FormBalancers produce incredibly complex shapes with details that were previously considered impossible to metal form.
FluidForming Americas offers a line of deep-draw sheet metal forming presses with forming areas ranging from 800 mm to 1,300 mm.
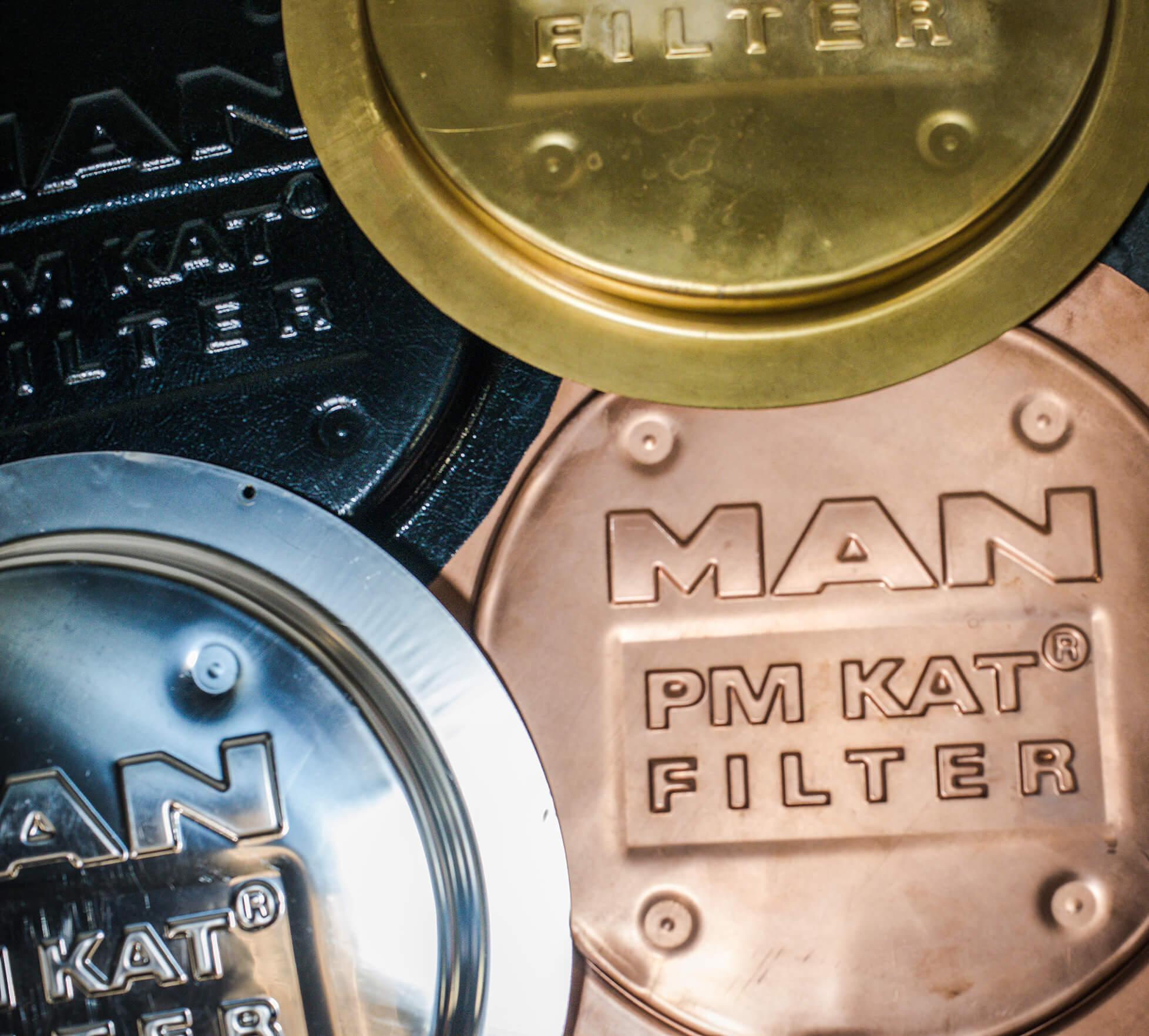
What metals are compatible with FluidForming?
FluidForming’s highly adaptable and flexible hydroforming process is the ideal solution to your most complex and troubling metal forming problems. No other hydroforming process boasts a 99.996% first-pass yield rate.
Our reinvention of the conventional deep-draw hydroforming process is highly compatible with a variety of metals, alloys, and superalloys. Even aluminum alloys, which are notoriously prone to wrinkling and fracturing under stress, perform well with the FluidForming technology and process.
- Aluminum
- Brass
- Bronze
- Carbon Steel
- Stainless Steel
- Copper
- Nickel
- Cobalt
- Hastelloy
- Inconel
- Lead
- Aluminum Alloys
- Molybdenum
- Nickel-based Superalloys
- Magnesium Alloys
- Titanium
- Tin
- Kovar
- Clad Metals
- Galvanized
- Pre-finished Metal