How the FluidForming Sheet Metal Hydroforming Process Works
The FluidForming Sheet Metal Hydroforming Process.
FluidForming is a modern reinvention of hydroforming, and our sheet metal hydroforming process has been trusted by leading American and European manufacturers for more than 20 years. Our sustainable metal forming process uses highly pressurized recycled tap water as the forming force and allows for precise rapid prototyping and low- to medium-volume parts production.
The Physics of FluidForming.
Every step of our sheet metal hydroforming process — from material flow to clamping pressure to water volume and pressure — is variable and controlled. Forming pressures of up to 4,000 bar (60,000 psi) ensure that FluidForming achieves finer, more detailed results than any other sheet metal hydroformg forming process available to manufacturers today. It's all about the physics.
The Fluidforming Sheet Metal Hydroforming Process.
Establish clamping pressure.
Introduce forming force.
Establish forming pressures.
With high forming pressures of up to 4,000 bar (60,000 psi) the sheet metal flows evenly into the form cavity.
Final forming stage.
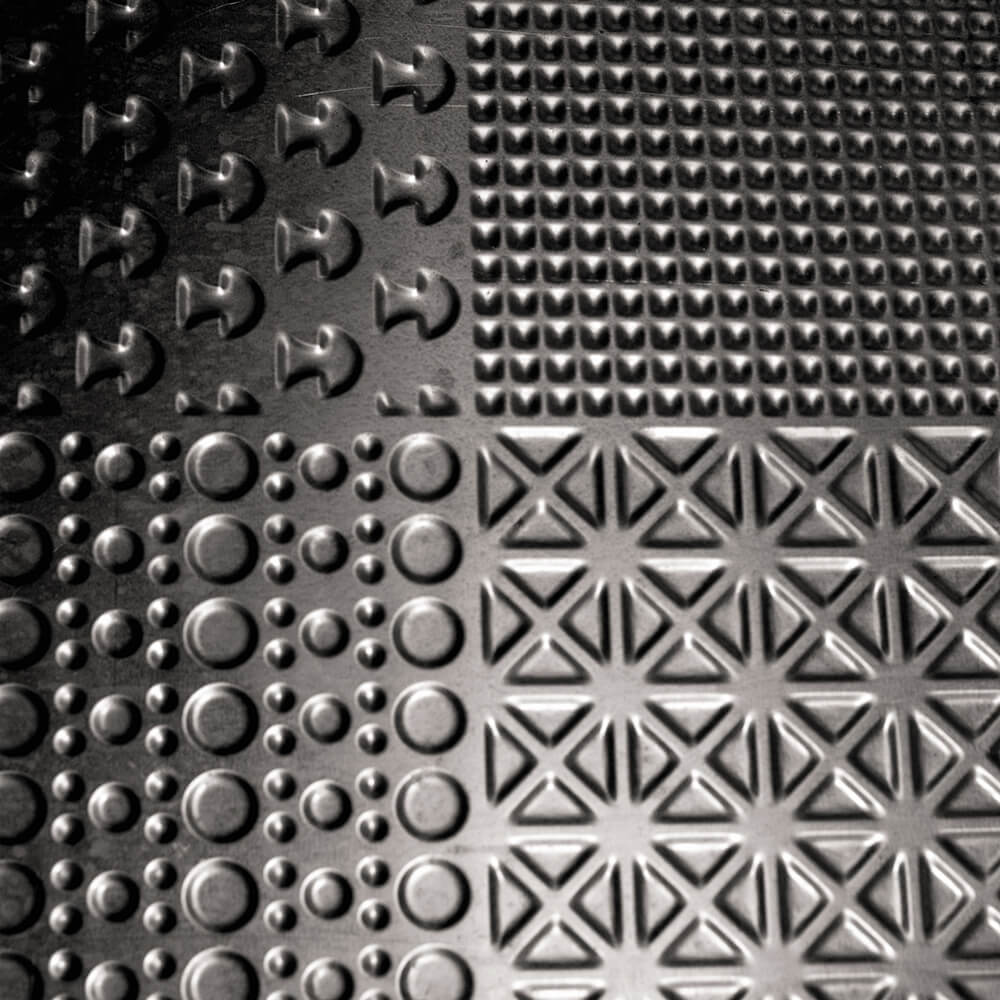
FluidForming's sheet metal hydrofrming process makes it possible to form complex, highly-detailed and defined components — with 99.996% accuracy and repeatability. Our manufacturing facilty can accommodate rapid prototyping and low- to medium-volume part production. FluidForming Americas can help companies form the "unfordable" at a lower overall cost.
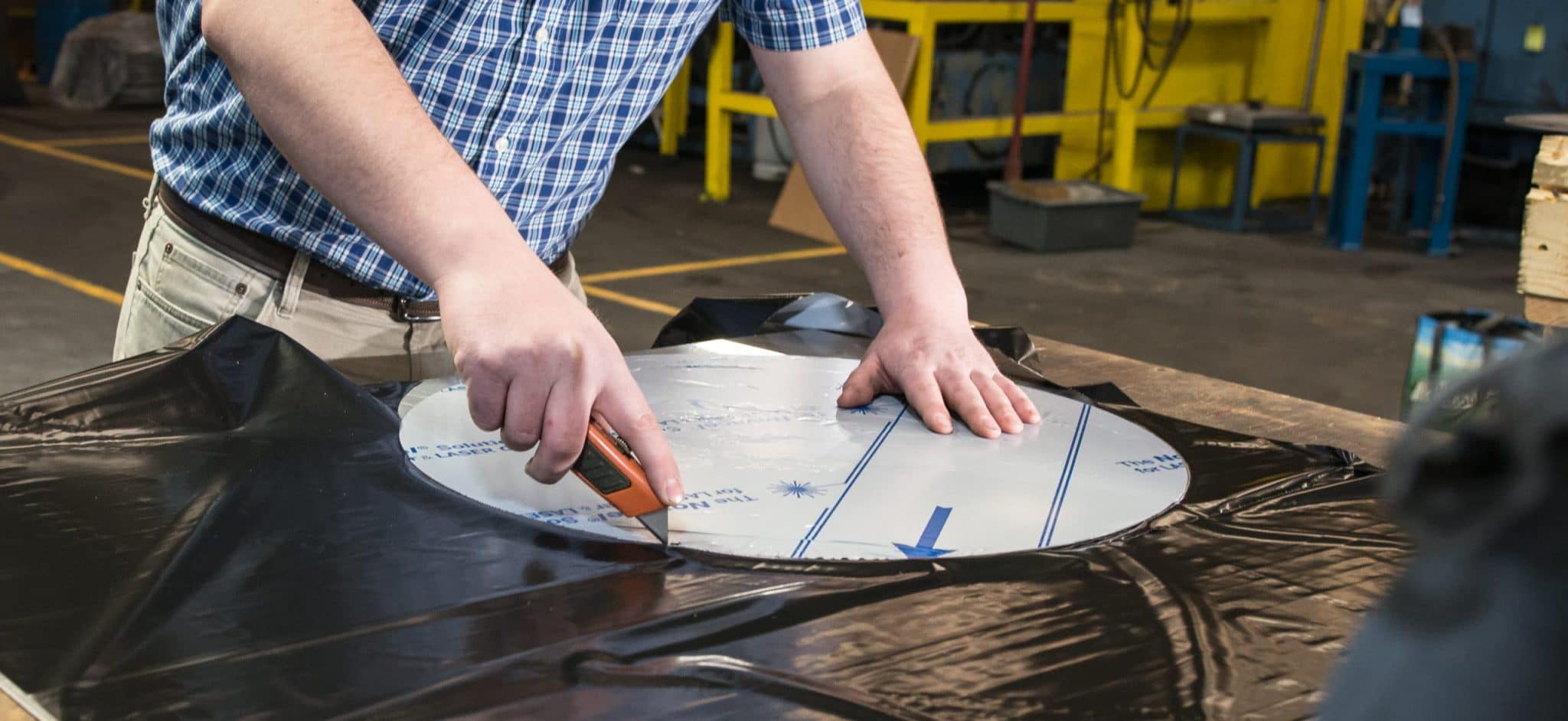