Sustainable Manufacturing & Hydroforming For the Automotive Industry
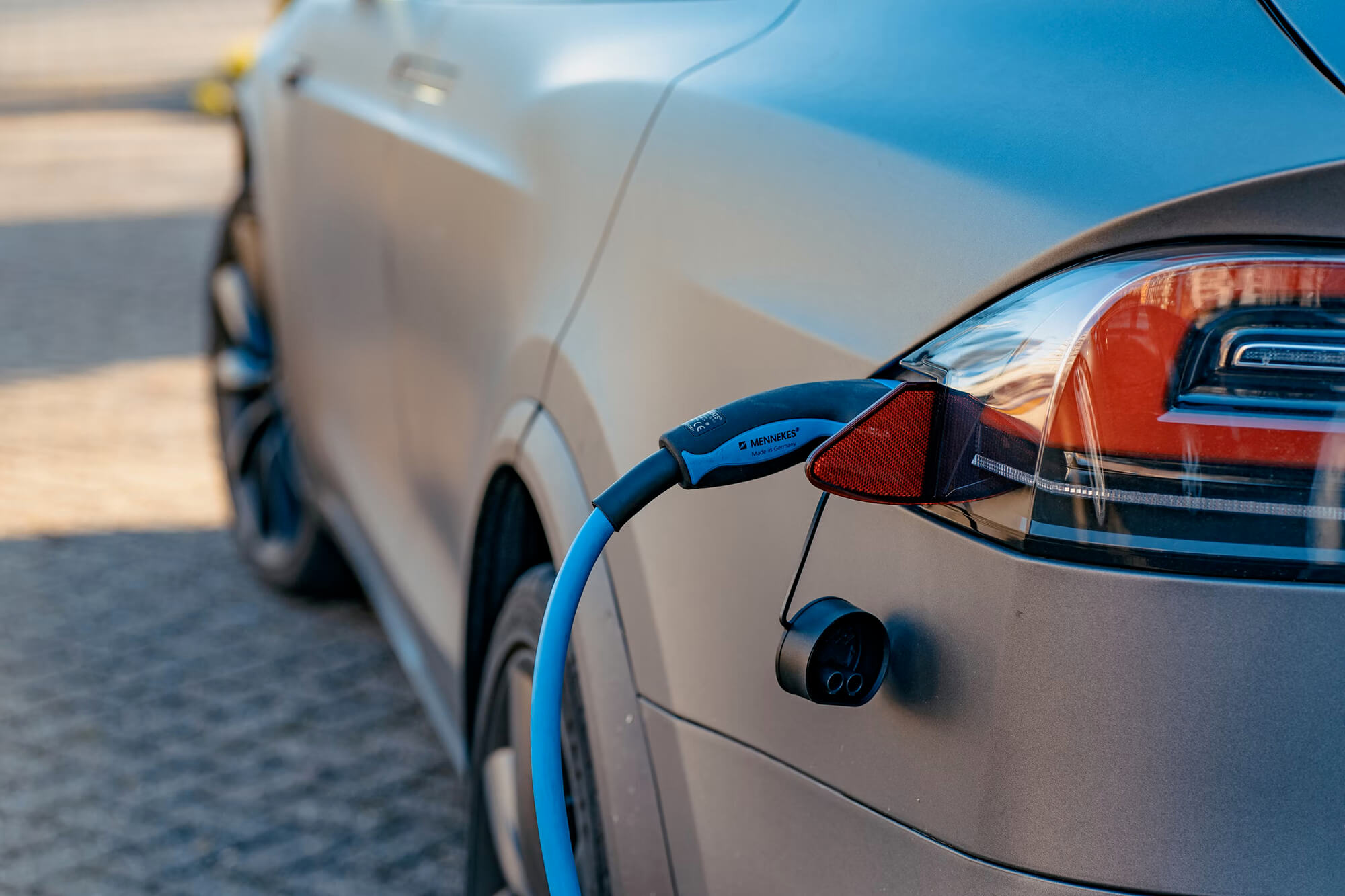
Environmentally-friendly Manufacturing For the Automotive Industry.
FluidForming's Made in America components help automakers build an economically strong foundation of automated, connected, efficient, and sustainable processes that minimize harmful environmental impacts while conserving energy and natural resources.
Fluidforming is an ideal prototyping solution for automakers because it delivers exceptional precision, speed, and flexibility. Unlike traditional stamping or hydroforming, fluidforming uses water at ultra-high pressures to create complex, high-tolerance parts in a single step—without costly tooling. This allows engineers to iterate quickly, test designs faster, and reduce development costs.
Whether refining a component’s shape or evaluating material performance, fluidforming accelerates innovation while maintaining the quality and repeatability the automotive industry demands. Plus, we made every part right here in Tennessee.
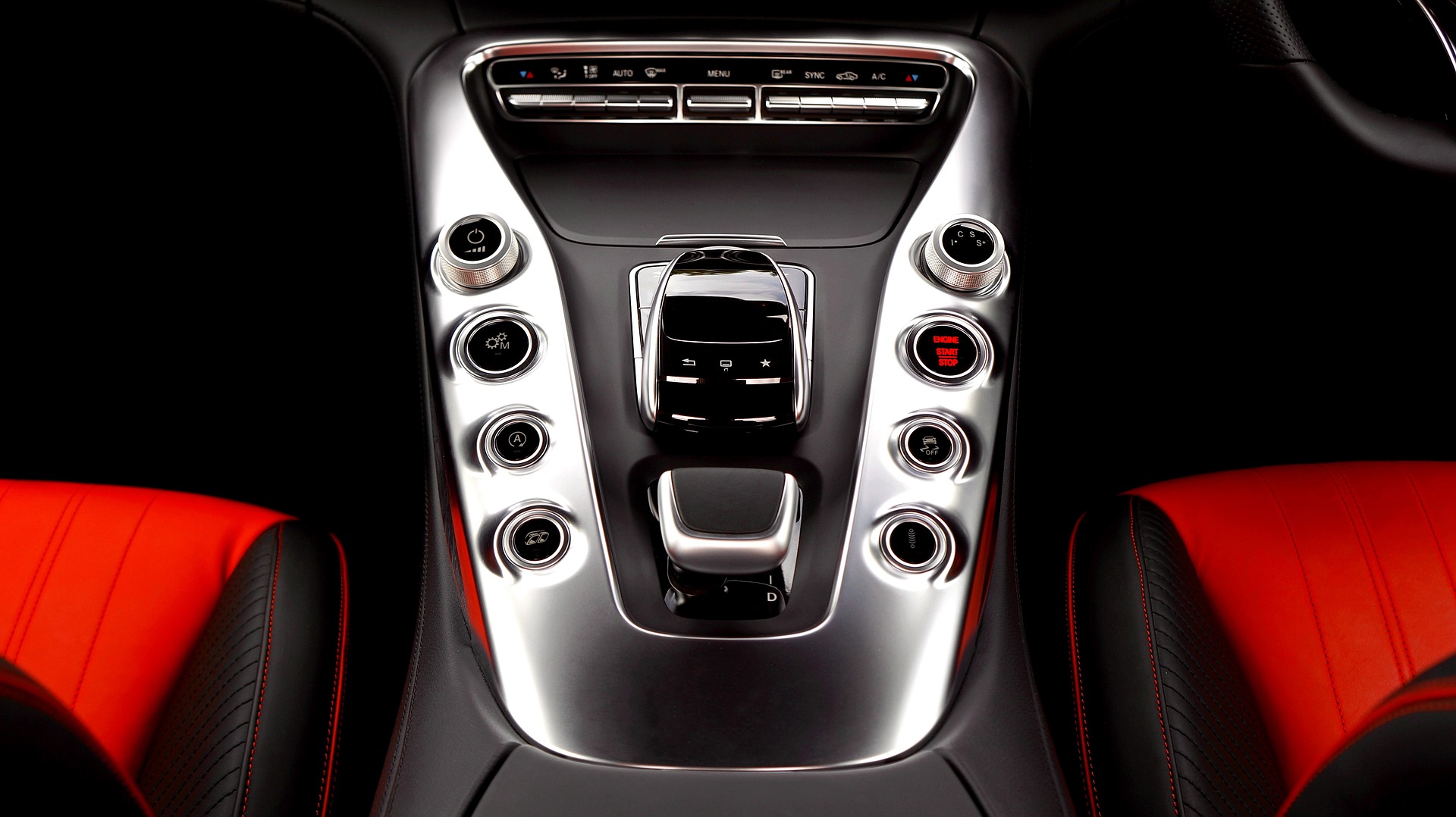
FluidForming Sheet Metal Hydroforming for Leading Automakers and OEMs.
FluidForming is a new and improved approach to traditional hydroforming — a sheet metal forming process that automakers have embraced for many decades.
Unlike legacy hydroforming, however, FluidForming enables cost-effective rapid prototyping and precision sheet metal forming. Making it the perfect solution for automotive prototyping and low- to medium volume part production. Our cutting-edge technology and process has formed metal components for automotive industry leaders like BMW, Porsche, and Mercedes-Benz.
The FormBalancer
A universal tube forming & sheet metal forming machine.
Whether an automaker is prototyping unibody panels or testing new performance intake manifolds, FluidForming’s universal sheet metal forming machine, the FormBalancer, can handle it.
The FormBalancer is a force-contained structure that permits extremely high forming pressures of up to 4,000 bar (60,000 psi). With up to 4x the pressure used by legacy hydroforming devices, high-performing automotive parts can be formed with ease.
Some parts that are commonly formed for the automotive industry include:
- Body panels
- Engine cradles
- Fan blades
- Manifolds
- Suspension components
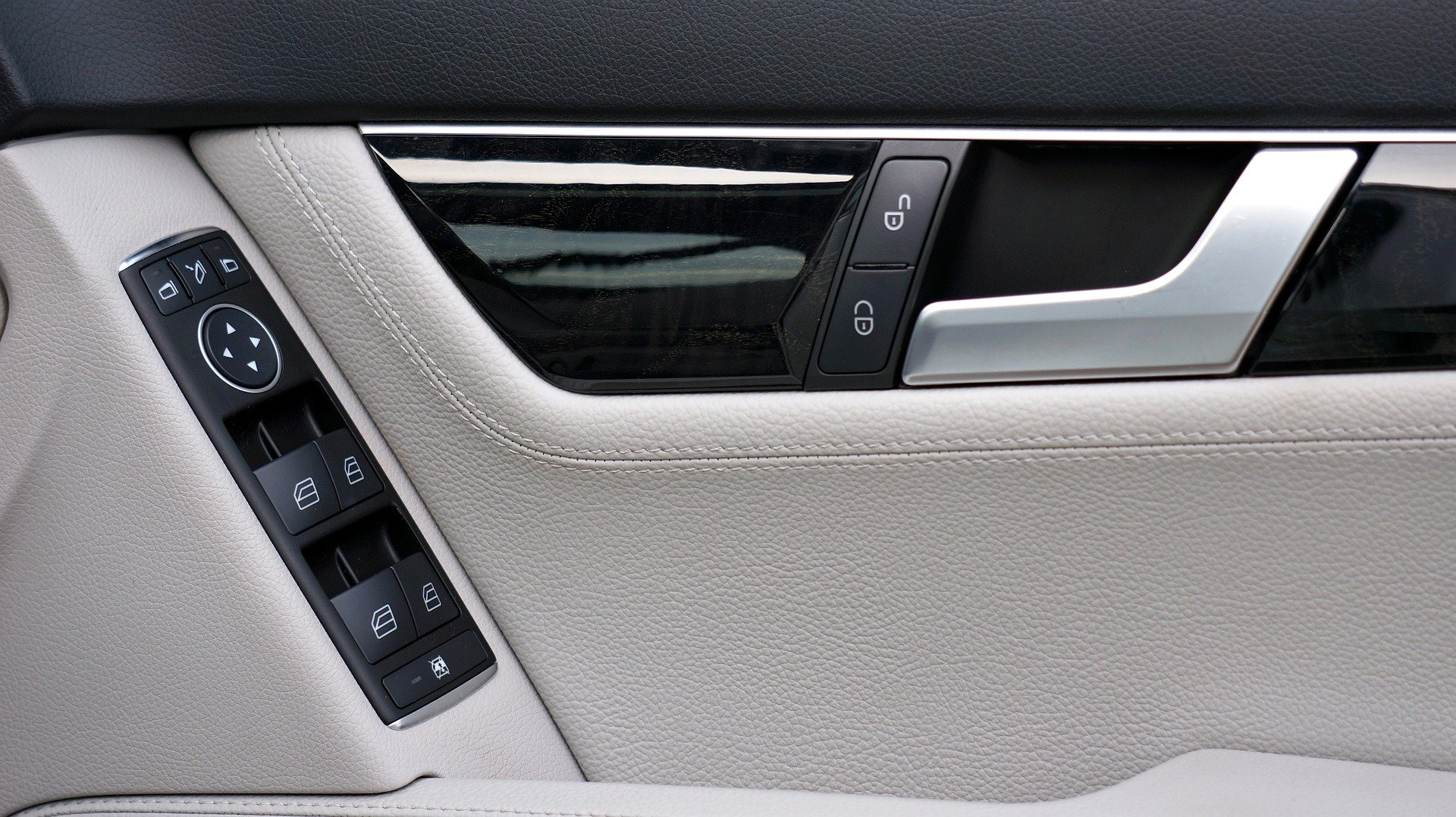
Benefits of FluidForming Hydroforming Within the Automotive Industry.
FluidForming’s innovative approach to hydroforming offers a number of potential benefits for automotive manufacturers.
Parts produced using the FluidForming technology are lightweight and durable. In many cases parts once manufactured with inferior plastics can now be formed with lightweight metal alloys. FluidForming is capable of forming metal from 1.01mm to 5 mm in thickness. These lightened components can also make a positive impact on fuel economy and performance.
Generally speaking, FluidForming produces unibody parts which exhibit a greater strength than that of conventionally welded joints or components. Other potential benefits of FluidForming in the automobile industry include increased component rigidity, reduced dimensional variability, and a reduction in the number of parts (or joints).
Driving Innovation & Advancement in the Auto Industry.
Automotive designers and engineers appreciate the increased design flexibility that our fast prototyping capabilities enable. With FluidForming, designers are able to innovate and iterate seamlessly.
FluidForming technology is ideal for rapid prototyping and low- to medium volume production with the ability to mass produce. With our technology, automotive designers enjoy shorter time-to-market and the ability to innovate freely. Because our system enables the transition from CAD to Finite Element Analysis (FE) to 3D-printed tooling, we’re able to move from design to production in days rather than weeks or even months.